Are you fascinated by the precision of metal parts in industries? Every intricate detail is made possible through the transformative process of CNC turning.
CNC turning is a manufacturing process that utilizes computer-controlled machines to remove material from a rotating workpiece, resulting in precise and intricate shapes. And on top of that, this process provides a reliable solution for industrial manufacturing, ensuring high production rates with exceptional precision.
In this article, we will explore the incredible potential of CNC turning, covering costs, benefits, and more.
If you’re ready to unlock the world of precision, read on and discover the power of CNC turning!
1. Brief Overview of CNC Turning
CNC Turning, an essential manufacturing technique, precisely sculpts material into desired forms, making it a fundamental process across various industries. Here’s why that’s important: CNC Turning, with its precise carving of rotating material, has proven to be a vital cornerstone across diverse industries. Its blend of technology and precision is simply remarkable.
CNC Turning plays a vital role in industries like automotive and aerospace, where precision is a necessity. Its adherence to strict specifications highlights its invaluable contribution to modern manufacturing. I think you’ll agree with me when I say that CNC Turning plays a vital role in industries where precision is not only preferred but also mandatory.
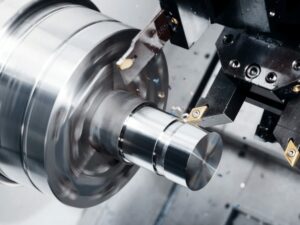
2. The Evolution of CNC Turning in Manufacturing
CNC turning, a cornerstone of manufacturing, has significantly evolved, transforming from traditional lathe work to an advanced process enabled by technology and automation. Here in the following, we are delving into the evolution of CNC turning in manufacturing:
The Dawn of CNC
The inception of CNC turning in the 1950s marked a momentous milestone in the manufacturing sector. It ushered in a new era where the rudimentary punch-tape systems, although slow by today’s standards, were undeniably revolutionary. Suprotos played a pivotal role in enhancing precision and repeatability, setting the stage for the remarkable advancements we witness today.
The Digital Revolution
The integration of computers during the digital age transformed CNC turning in the late 20th century. This revolutionized the programming process, significantly improving operational efficiency. From my own experience, I witnessed the transformative phase of CNC turning during the late 20th century when computers were integrated into the process, marking a significant turning point.
The Age of Automation
Today, with the rise of Industry 4.0 and IoT, CNC-turning machines have entered a new era of intelligence and connectivity, revolutionizing manufacturing operations like never before. Here’s something we can both agree on: the integration of Industry 4.0 principles and IoT technology into CNC-turning machines has been truly transformative.
3. Types of CNC Turning
CNC Turning, a process where material bars are rotated and shaped by tools, is great for making cylindrical parts. Different CNC turning types cater to varying design and production needs. The types of CNC turning processes we’re going to dissect are listed below:
Straight Turning
Straight turning removes material from the workpiece’s external surface, shaping it into a cylindrical form. This process’s precision and repeatability have made it widely favored across industries. So what’s my point? Straight turning, from my own experience as a CNC manufacturer, is a technique that I have come to appreciate for its simplicity and effectiveness. It precisely shapes the workpiece into a cylinder.
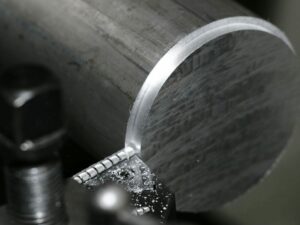
Taper Turning
This method carves a conical shape on the workpiece. It’s crucial for creating parts with angular surfaces in the automotive industry for the production of transmission shafts. You don’t want to miss this next part: from my own experience as a CNC manufacturer, I’ve witnessed the significance of taper turning in creating parts with angular surfaces, which is crucial for automotive manufacturing.
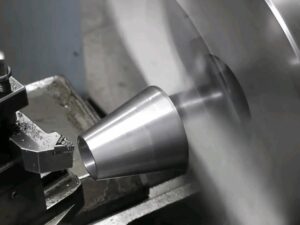
Profile Turning
Profile turning is a versatile technique used to craft intricate contours and profiles on workpieces. This method plays a crucial role in the production of complex components, especially those found in critical industries like medical device manufacturing. The ability to accurately shape intricate profiles through profile turning enables the creation of precise and customized parts that meet the stringent requirements of various applications.
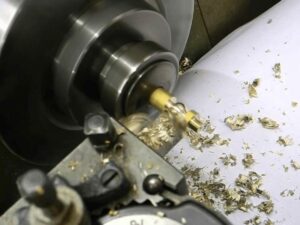
Hard Turning
Hard turning is specifically tailored for the machining of tough materials that pose challenges for traditional methods. This technique excels in handling hardened materials where conventional machining techniques struggle to deliver the desired results. What makes hard turning even more remarkable is its eco-friendly nature.
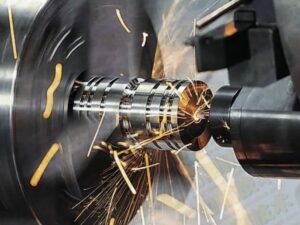
4. Core Components of a CNC Turning Machine
CNC turning machines are integral in manufacturing, streamlining the creation of precise, symmetrical parts. These machines automate cutting, sanding, and drilling tasks, with key components making them highly functional. Detailed below are the components that give these machines their versatility and efficiency:
Machine Bed and Guide Ways
The bed serves as the solid foundation of the machine, imparting stability and support throughout the machining process. It acts as a crucial anchor, ensuring optimal rigidity and vibration damping. Meanwhile, guideways play a vital role in facilitating the precise movement of both the tool and workpiece. These components enable precise tool movement, allowing for intricate shaping and exceptional accuracy.
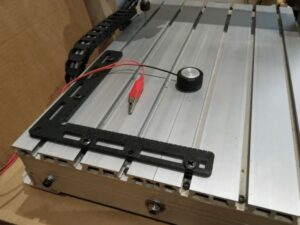
The CNC Controller
The CNC controller, often referred to as the “brain” of the machine, is the core component responsible for controlling all movements and operations with utmost precision. It is the Suprotos CNC controller that serves as central intelligence, orchestrating seamless coordination between various machine components. It enables CNC turning machines to execute intricate tasks with exceptional precision.
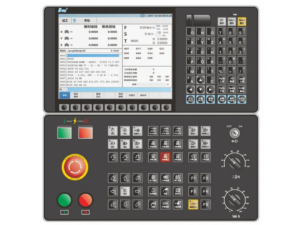
Spindle and Chuck
The spindle and chuck form a vital duo in CNC turning machines. The spindle takes charge of rotating the workpiece, ensuring precise rotational movement during the machining process. The chuck ensures workpiece stability for accurate machining operations. For example, the spindle’s rotation and the chuck’s grip work together to create precise cylindrical components.
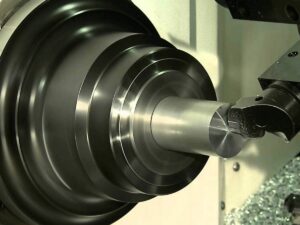
Tool Turret
The tool turret, a crucial component of CNC turning machines, enables efficient operations by holding various tools and eliminating the need for manual changes during multiple operations. Now, this is important: the tool turret’s incredible capabilities have a profound impact on productivity and downtime reduction, as I’ve seen in my experience as a CNC manufacturer.
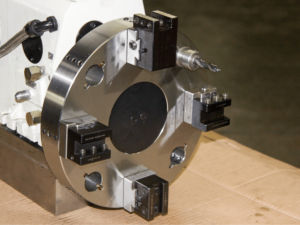
Tailstock
The tailstock is crucial in CNC turning as it provides essential support to the workpiece, preventing bending or distortion during machining operations. And the best part is, in my experience as a CNC manufacturer, I’ve witnessed firsthand how the tailstock’s firm grip ensures precise and accurate cuts, resulting in high-quality finished parts.
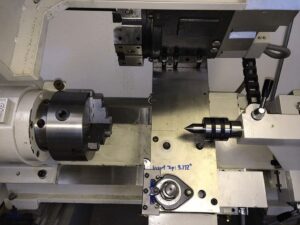
5. The CNC Turning Process: Step-by-step Guide
CNC turning, a fundamental in modern manufacturing, enables the production of precise, complex parts through a computer-controlled process. It involves shaping a rotating workpiece with a cutting tool, guided by CAD or CAM files. Below, we outline the step-by-step processes in CNC turning:
Step #1 Planning and Design
The initial step in the CNC turning process involves the creation of a detailed 3D model of the desired part using sophisticated CAD software. This crucial step allows engineers and designers to precisely define the dimensions and tolerances required for the final component. For example, in the automotive industry, manufacturers utilize CAD technology to create a detailed 3D model of engine components.
Step #2 Setting up the CNC machine
After the 3D model is prepared, the next step in CNC turning is machine setup. The operator installs the workpiece onto the chuck or collet, ensuring secure and precise positioning. And now, you’re thinking, “What is the pivotal role of the operator in the CNC turning setup process?” Well, from my own experience as a CNC manufacturer, let me tell you that the operator’s role is absolutely crucial.
Step #3 The Actual Turning Process
Once the setup is complete, the CNC machine takes center stage, expertly shaping the workpiece according to programmed instructions with remarkable precision. I’m sure you’re with me on this one —from my own experience as a CNC manufacturer, I’ve witnessed the remarkable benefits of CNC machining. The machine executes programmed commands with unfailing precision, delivering exceptional results.
Step #4 Post-Turning Operations
Upon completion of the turning process, the part enters a crucial phase of finishing operations, which includes essential steps like a thorough cleaning and meticulous inspection. Following the cleaning process, a comprehensive inspection is conducted to verify dimensional accuracy, surface quality, and overall conformity to the required specifications.
6. CNC Turning Tools and their Applications
CNC turning tools enable precise machining, shaping intricate designs with high quality. Paired with CNC turning machines, they remove material from rotating workpieces. Each tool type has specific applications and advantages. Here, we delve into the tools and their specific applications:
Cutting Tools
Cutting tools are the workhorses of CNC turning, efficiently removing material, and shaping the workpiece to achieve the desired form. The selection of the appropriate tools holds immense importance as it directly impacts the finish and dimensional accuracy of the final part. For instance, factors like tool geometry, cutting speed, and feed rate are carefully considered to achieve optimal results.
Boring Tools
Boring tools are essential in CNC turning for enlarging and refining holes, resulting in accurate and smoother surfaces. Here’s the bottom line: from my experience as a CNC manufacturer, boring tools play an invaluable role in CNC turning. They enable manufacturers to achieve precise dimensional accuracy, roundness, and surface quality for critical components.
Drilling Tools
This process is particularly crucial for parts that demand precise hole placements, such as engine blocks or cylinder heads. Here’s the interesting part: drilling tools showcase remarkable capabilities in CNC turning operations. These tools excel in creating various types of holes, including coolant passages, bolt holes, and intricate patterns, with unmatched precision and reliability.
7. CNC Turning vs. Traditional Turning: Key Differences
CNC turning and traditional turning are distinct methods for machining cylindrical workpieces. While both involve shaping the material, they differ in operation, control, and efficiency. Understanding these key differences is vital for selecting the appropriate approach. Below, we explore these differences and compare the tools used in each method:
Precision and Consistency
CNC turning provides higher precision and consistency than traditional turning due to its computer-controlled operation. A key factor to consider is the ability of CNC turning to maintain tolerances within a few micrometers. You guessed it —I’ve come to appreciate that CNC turning offers exceptional precision and consistency compared to traditional methods, due to its computer-controlled operation.
Automation and Productivity
CNC turning presents an opportunity for manufacturers to automate their processes, resulting in heightened productivity and significant reductions in labor costs. And then it hit me — as a CNC manufacturer, I realized the tremendous benefits that automation brings to CNC turning processes. It not only boosts efficiency but also frees up valuable resources for more complex tasks.
Flexibility
CNC turning provides unparalleled flexibility, enabling seamless adaptation to design changes without the need for physical adjustments to the machine. According to HLH Rapid, CNC machining offers remarkable versatility, capable of working with a wide range of plastic and metal alloys. This flexibility enables prototyping in virtually any material required, making it an invaluable tool in various stages of the rapid prototyping (RP) process.
The following table highlights the unparalleled flexibility of CNC turning, showcasing its adaptability to design changes, versatility with various materials, and its crucial role in rapid prototyping.
Aspect |
Description |
Adaptability |
CNC turning allows for seamless adaptation to design changes without requiring physical adjustments. |
Material Versatility |
CNC machining is capable of working with a wide range of plastic and metal alloys. |
Prototyping |
CNC turning enables prototyping in virtually any material required, facilitating rapid prototyping. |
Rapid Prototyping |
CNC turning is an invaluable tool in various stages of the rapid prototyping (RP) process. |
8. Troubleshooting Common CNC Turning Issues
Troubleshooting common CNC turning issues is vital for maintaining efficient and accurate machining operations. Various challenges can impact the quality of finished parts. In the following subsections, we explore common issues and the tools used to troubleshoot them effectively. Below, we’ll discuss the tools and common issues encountered in CNC turning:
Tool Breakage
Regular inspections and timely tool replacements effectively mitigate the challenge of tool breakage in CNC turning, minimizing production disruptions and workpiece damage. Then it finally dawned on me: from my own experience as a CNC manufacturer, I’ve learned the importance of proactive maintenance and vigilant monitoring in CNC turning operations.
Inaccurate Cuts
Issues in CNC turning can arise due to factors like tool wear, improper tool selection, or incorrect machine setup. Using a cutting tool with incorrect geometry can lead to inaccurate cuts, compromising precision. But guess what I realized just in the nick of time – meticulous machine setup in CNC turning is crucial. Even slight misalignments or tool positioning issues can cause significant setbacks.
Machine Vibrations
CNC turning provides unparalleled flexibility, enabling seamless adaptation to design changes without the need for physical adjustments to the machine. As stated by Sans Machining, machining vibration, commonly referred to as chatter, is the occurrence of undesired vibrations that arise during cutting operations in machining processes like CNC milling, turning, and drilling.
Improper Finishes
Improper finishes can stem from a variety of factors, including incorrect cutting speeds, improper tool selection, or machine malfunctions. Inadequate control over cutting speeds can lead to rough or uneven surfaces, while incorrect tool selection may result in poor surface quality. Moreover, machine malfunctions, such as issues with coolant flow or spindle misalignment, can also contribute to subpar finishes.
Dive Deeper Into Our Resources
For some insightful reads, we’ve curated a list of recommended articles just for you:
Still haven’t found what you’re looking for? Don’t hesitate to contact us. We’re available around the clock to assist you.
Conclusion
In conclusion, the significance of meticulous machine setup in CNC turning cannot be emphasized enough. Even slight misalignments or tool positioning issues can cause significant setbacks, jeopardizing the overall precision and quality of the machining process.
Therefore, it is imperative for manufacturers to prioritize meticulous machine setup to ensure optimal performance and avoid costly deviations. Based on my experience, investing time and effort in precise machine setups will pay off in the form of enhanced accuracy and productivity. Contact us today and let Suprotos assist you in achieving impeccable machine setup in your CNC turning operations.