Can manufacturers fathom the digital age where intricate parts materialize seamlessly, unlocking an era free from manual constraints? But wait, it’s not the realm of fantasy but an everyday reality through the marvels of CNC machining. However, as industries evolve, the need for precision, efficiency, and versatility in manufacturing escalates.
CNC machining caters to these exact demands, with its adaptability to handling a plethora of materials, making it indispensable across diverse industries such as aerospace, automotive, and medical. From creating aircraft parts to custom car components, the applications of CNC machining are virtually limitless.
Intrigued? Read on and join me as we delve into the astonishing world of CNC machining and its multifaceted applications.
1. Brief Overview of CNC Machining
Welcome to the marvels of the modern manufacturing world! Today, the shining spotlight on the rock star of precision part manufacturing – CNC Machining. Like a maestro conducting an orchestra, CNC, which stands for Computer Numerical Control, is a technology that precisely maneuvers cutting tools to sculpt away material from a solid block, giving birth to a symphony of shapes and designs in metals and plastics.
For me, it is the darling of industries like aerospace, automotive, and medical equipment where precision is as crucial as a heartbeat. The most sought-after versions of this superstar tech are CNC Milling and Turning. Milling, the fan-favorite, employs a spinning tool to cut through material as it moves across the block, while Turning is the graceful ballerina that spins the material block against a static cutting tool.
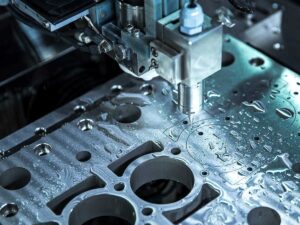
2. The Evolution of CNC Machining
As an expert in CNC machining, CNC machining has become an essential tool in various industries, including aerospace, healthcare, and consumer electronics. Here’s a guide through the fascinating journey of CNC machining, from its inception to the marvels of modern technology.
Early Beginnings
The story of CNC machining began in the early 1940s, with the development of Numerical Control (NC) machines. John Parsons is credited with inventing the first NC machine, which operated using punch cards for controlling movement. However, the breakthrough came in 1952, when the first CNC machine was developed at MIT. This revolutionized the manufacturing industry by transitioning from manual to automated control.
Middle Ages
During the subsequent decades, CNC technology saw significant advancements. The early punch tape-controlled devices evolved into computer-programmable machines. This evolution allowed for increased precision and flexibility in manufacturing. The integration of advanced robotics systems into CNC machines in the latter part of the 20th century dramatically enhanced productivity and reduced labor requirements.
Present
Fast-forward to the present day, CNC machining boasts impressive computerized features, thanks to constant developments over the years. Modern CNC machinery boasts superior speeds, accuracy, and automated precision, which are crucial in industries like aviation that require high-precision manufacturing processes. As I can see, CNC machining now supports a wide range of materials and advancements.
3. Types of CNC Machines
Understanding the range and capabilities of CNC machines is critical for anyone involved in manufacturing or construction. Let’s dive into the versatile world of Computer Numerical Control with a guide to the types of CNC machines. Here they are:
CNC Mills
Let’s talk about CNC Mills, which are indeed the crème de la crème of CNC machines. CNC mills are primarily used for milling, drilling, and cutting operations. They are versatile workhorses that derive instructions from specific programs made up of letters and numbers, known as G-code. Worth mentioning is the pioneer in CNC Mills, Suproto, whose name is synonymous with precision and reliability in the machining world.
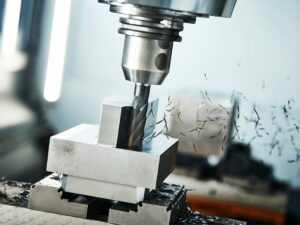
CNC Lathes
Now, let’s pivot to CNC Lathes. When it comes to turning materials during operation, CNC lathes steal the show. What makes them unique is their fewer axes compared to CNC mills, which renders them more compact. We have witnessed at Suproto, that CNC Lathes are extremely efficient and, once the initial setup is done, even a semi-skilled worker can operate them effortlessly.
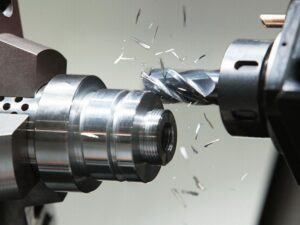
CNC Routers
Shifting gears to CNC Routers, these machines are somewhat similar to CNC mills but are generally used for machining softer materials such as wood, foam, and plastics. Unlike CNC mills, CNC routers are typically less precise but are excellent for projects that don’t require the utmost accuracy.
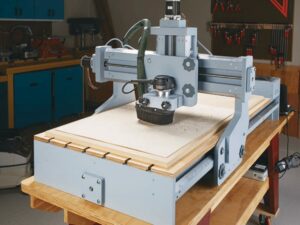
CNC Plasma Cutters
Forging ahead is the CNC Plasma Cutters. As the name suggests, these machines employ plasma cutting technology to cut through electrically conductive materials, such as steel and aluminum. I can tell, they work by sending an electric arc through a gas that is passing through a constricted opening.
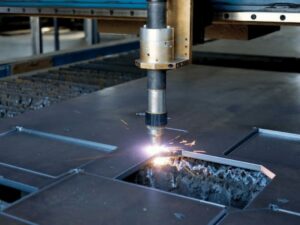
CNC Laser Cutters
According to Absolute Reports, the global laser cutting machine market is valued at 3.37 billion USD in 2020 and is expected to reach 6.69 billion USD by the end of 2027, growing at a CAGR of 10.65% during 2021-2027. These machines are the epitome of precision and speed. CNC laser cutters employ laser technology to cut materials, ranging from metal to plastic.
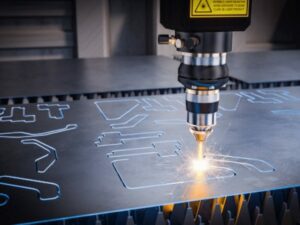
4. Materials Compatible with CNC Machining
When it comes to CNC machining, selecting the right material is just as important as choosing the right machine. Explore various materials and how their properties make them suitable or unsuitable for specific CNC machining applications. Below are the ff:
Metals
Metals are the backbone of CNC machining and are often selected for applications that require high strength, hardness, and thermal resistance. I can tell they are also popular due to their machinability. Light metals such as aluminum, brass, and copper boast high machinability, which means that they can be efficiently shaped by CNC machines with minimal wear on the cutting tools.
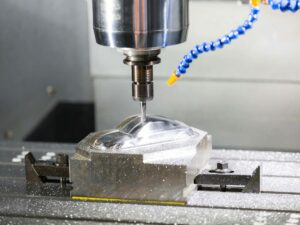
Plastics
Moving on, plastics are another versatile material category in CNC machining. They are lighter than metals and offer a range of physical properties, including chemical resistance and electrical insulation. Notably, some plastics have high machinability, which is advantageous for productivity and part quality. It’s imperative to be mindful of the fact that certain plastics, like carbon fiber composites, can be tough to machine.
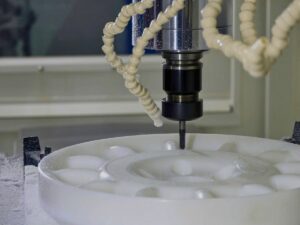
Wood
Let’s not forget about wood, a classic material that has been shaped by tools for centuries. In the context of CNC machining, wood offers a blend of aesthetic appeal and functionality. Speaking from experience, I have witnessed that it is less commonly used compared to metals and plastics, but it still holds a significant place, especially in the furniture and decorative items industry.
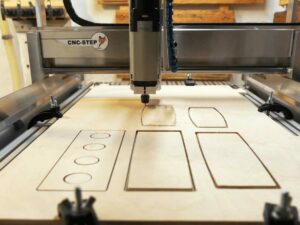
Composites
Transitioning into the realm of composites, these materials are engineered by combining two or more materials, hence offering unique properties not present in individual constituents. Carbon fiber composites, for example, are highly valued for their strength and lightweight properties but can be challenging to machine due to their toughness.
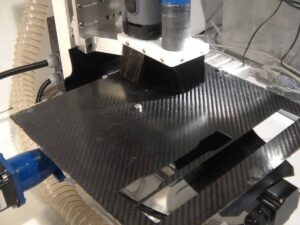
Glass and Ceramics
Glass and ceramics are intriguing materials that can be used in CNC machining. Generally, these materials are harder and more brittle, which means they require specialized machining techniques. Moreover, their applications are niche, often used in industries where hardness, thermal resistance, or electrical insulation are paramount.
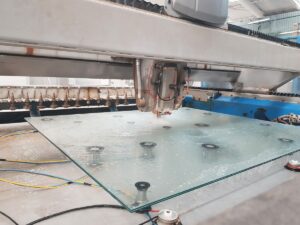
5. Industries Utilizing CNC Machining
The precision and efficiency of CNC machining have made it indispensable across a myriad of industries. Uncover the vital role that CNC machining keeps the modern world turning. Here are some to explore:
Aerospace and Defense
The aerospace sector, in particular, requires parts with unparalleled precision and reliability, as the slightest error can have catastrophic consequences. CNC machining makes it possible to produce these high-tolerance, complex components with remarkable consistency. Additionally, CNC machining has historical roots in the aerospace industry, first being developed during World War II for creating aircraft replacement parts.
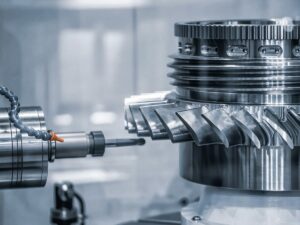
Medical Devices
Next is the medical device sector where the demand for precision is equally critical. The production of medical screws, for instance, requires absolute accuracy, as these components are integral to various medical procedures. I can vouch, CNC machining technology has proven invaluable in this regard. About 900 million medical screws are needed annually, and CNC machining has proven itself in meeting this demand.
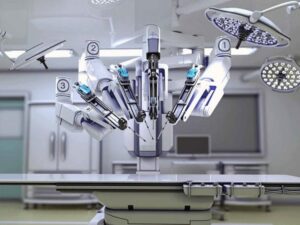
Automotive Industry
The automotive sector necessitates components with precise measurements to ensure safety and performance. CNC machining offers not only the required precision but also the ability to produce parts in high volumes, which is essential for an industry characterized by mass production. The adaptability of CNC programmable machine tools also enables efficient production of diverse components within the same batch.
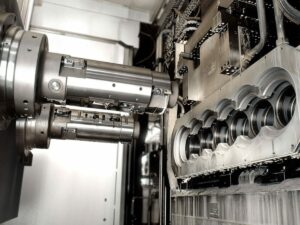
Construction and Architecture
CNC machining has been transformative in the construction and architecture realm. With its ability to work on a variety of materials, from metals to plastics, and create custom designs, CNC technology is instrumental in creating intricate architectural elements and robust construction materials.
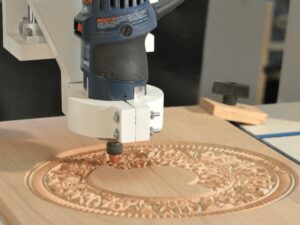
Electronics
The electronics industry is also reaping the benefits of CNC machining. I have witnessed precision and miniaturization are paramount in electronics, where components are becoming increasingly smaller and more complex. CNC machining is adept at producing tiny, intricate parts, and is, therefore, a crucial tool in the electronics industry’s arsenal.
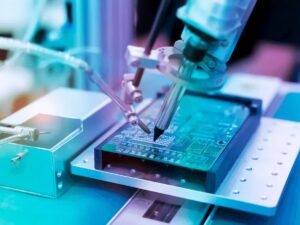
6. CNC Machining Processes
CNC machining processes play a pivotal role in shaping numerous industries. Let’s take a closer look at each step involved in CNC machining processes, and discover how they contribute to the manufacturing of intricate components.
Step#1 Milling
An essential part of the CNC machining process is milling. It involves using a cutting tool to remove material from a workpiece. By rotating and moving the cutting tool across the surface of the material, intricate shapes and details are carved out. Now, creativity doesn’t stop there! Milling is supremely versatile, being applicable to a plethora of materials ranging from metals to plastics.
Step#2 Turning
Next in line is the incredible turning process. Similar to milling, turning also involves the removal of material. However, in turning, the workpiece is the one that rotates instead of the cutting tool. Trust me, this process is especially favored when it comes to producing cylindrical or round parts.
Step#3 Drilling
This process involves creating round holes in a workpiece. CNC drilling utilizes various drill bits to achieve precise depths and diameters. This process is integral in numerous applications including the manufacturing of medical instruments. For example, California-based medical technology developer Galen Robotics employs CNC drilling to produce parts for technology that stabilizes a surgeon’s hands during delicate operations.
Step#4 Grinding
Moving on, let’s explore the realm of grinding. This process is used to refine the surface finish of a part or to bring it to a very specific size. Grinding uses an abrasive wheel as the cutting tool, which removes small chips of material from the workpiece. With the capability to achieve extremely tight tolerances and fine finishes, grinding is indispensable in applications where precision is paramount.
Step#5 Boring
Boring is a process where an existing hole is enlarged or finished with improved concentricity. This is usually achieved by using a single-point cutting tool or a boring head containing several cutting tools that can be adjusted to achieve the desired size and finish. The precision and finish achieved through boring are crucial in applications where holes must maintain strict tolerances for proper assembly and operation.
7. The Impact of CNC Machining on Manufacturing
From drastically reducing production times to enhancing accuracy and repeatability, CNC machining has reshaped manufacturing processes around the world. Now let’s delve into its profound impact on the manufacturing industry listed below.
Speed and Efficiency
CNC machining has revolutionized the manufacturing industry by significantly enhancing speed and efficiency. In the fast-paced world of advanced manufacturing, CNC machining stands as a pillar of efficiency, delivering remarkable speed and reliability. By operating continuously, these machines drastically reduce downtime, thus streamlining production processes.
The following table highlights the key aspects of speed and efficiency in CNC machining, showcasing its ability to revolutionize manufacturing processes through high-speed operations, continuous operation, streamlined production, and reduced downtime.
Aspect |
Description |
Speed |
CNC machining offers high-speed operations, allowing for quick production of parts and components. This speed is achieved through the automated and precise movements of the machine tools, reducing manual labor time. |
Efficiency |
CNC machines are designed for optimal efficiency in manufacturing. They eliminate human error, resulting in consistent and accurate output. Additionally, these machines can perform multiple operations in a single setup, reducing the need for manual intervention and setup changes. |
Continuous Operation |
CNC machines can operate continuously, 24/7, with minimal breaks or downtime. This uninterrupted operation improves overall productivity and throughput by maximizing machine utilization. |
Streamlined Production Processes |
CNC machining streamlines production by automating various tasks. It eliminates the need for manual tool changes, reduces setup time, and enables faster production cycle times. This streamlining of processes leads to increased overall efficiency. |
Reduced Downtime |
CNC machines have reduced downtime due to their reliability and automated capabilities. Maintenance and tool changeovers can be scheduled during off-peak hours, minimizing production interruptions. Additionally, the use of advanced monitoring systems can detect issues early, preventing unexpected breakdowns and reducing downtime. |
Scalability |
CNC machining offers scalability in production. Once the machine program is developed, it can be replicated and applied to multiple machines, enabling high-volume production without compromising speed or efficiency. |
Quality Control |
CNC machines provide precise and repeatable results, ensuring consistent quality in the manufactured parts. The automated nature of CNC machining reduces the likelihood of human errors, enhancing quality control in the production process. |
Versatility |
CNC machines can be programmed to produce a wide range of complex parts and components. Their versatility allows for the efficient machining of different materials, shapes, and sizes, making them adaptable to various manufacturing requirements. |
Waste Reduction |
CNC machining minimizes material waste by optimizing tool paths and cutting strategies. The precision and accuracy of CNC machines help maximize material utilization, reducing scrap and overall waste generated during the manufacturing process. |
Cost-Effectiveness |
The speed and efficiency of CNC machining contribute to its cost-effectiveness. By reducing labor costs, increasing productivity, and minimizing errors and waste, CNC machining offers a competitive advantage in terms of cost per part or component produced. |
Precision and Accuracy
In the realm of advanced manufacturing, precision, and accuracy are non-negotiable. CNC machining excels in this domain, providing unparalleled levels of accuracy, repeatability, and control. Through computer programming, these machines meticulously cut, shape, and mold materials into intricate designs with tight tolerances. For me, such levels of precision are indispensable.
Automation and Labour Reduction
Automation has been a game-changer in the industry. CNC machining’s automated processes not only enhance productivity but also alleviate the strain caused by labor shortages. By employing robotics, CNC machines can be programmed for various machining needs, rendering them flexible and adept at handling both high and low-volume projects. Plus, in my view, automation addresses the repetitive and heavy-lifting aspects of machining.
Cost-Effectiveness and Waste Reduction
Furthermore, cost-effectiveness and waste reduction are prominent benefits of CNC machining. By automating most of its processes, CNC machines significantly reduce the likelihood of costly human errors and material wastage. As a result of their precision and ability to run uninterrupted, there is a notable decrease in material waste. Thus, businesses not only save on material costs but also contribute to the environment.
Customization and Prototyping
Due to their incredible accuracy and material versatility, CNC machines have made it easier for designers and engineers to prototype and customize products without extensive manual labor. Moreover, with a company like Suproto specializing in CNC machining, manufacturers can leverage cutting-edge technology to bring their creative designs to life while ensuring top-notch quality and precision.
Conclusion
Throughout this blog, we’ve journeyed into the intricate realm of CNC machining, unearthing its historic roots and witnessing its transformative power in today’s industries. Whether it’s aerospace, automotive, or medical devices, CNC’s precise and adaptable capabilities are leading the charge.
Want to know how to leverage the multifaceted capabilities of CNC machining to advance the business and innovate in the field? Ready to take the leap or curious to explore further? We’re here to provide consultation and guidance tailored to every need. Remember, in the ever-evolving world of CNC machining, the next solution is just a consultation away. Contact us and let’s embark on this innovative journey together.