Thinking of creating impeccable wooden engravings or precision-milled metal parts for the business? Imagine the perfect piece of artistry – wooden engravings or precise metal parts that capture everyone’s gaze. But the fear of human error looms over the creative spirit when thinking of using conventional tools.
CNC Routing is that gallant champion! This computer-controlled cutting wizard brings accuracy and efficiency to the table, eliminating the stress of manual errors in creating intricate patterns and designs. In this article, we will unveil the secrets of CNC Routing, be a partner guide through the different types and essentials of the process, and ultimately empower business visions to craft perfection.
Ready to become the CNC maestro? Let’s dive in and read on!
1. A Brief Overview of CNC Routing
CNC Routers, the spellbinders themselves, are computer-controlled cutting machines that can shape a multitude of materials like wood, metals, plastics, and even foams into intricate patterns and designs. Trust me, with a flick of a program, the CNC router is like a magical ride from a piece of material to a symphony of cuts and carves. The CNC router is one of many kinds of tools that have CNC variants.
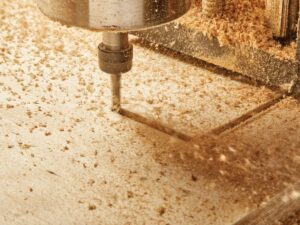
2. The History and Evolution of CNC Routing
CNC routing, I believe, started to create wonders in the industry many years ago. Now, let’s travel through time to see how this revolutionary technology evolved over the centuries.
Early Beginnings
In the early days, the automation of machine tools began with cams that mechanically “played” a machine tool. These mechanisms were akin to those found in musical boxes or elaborate cuckoo clocks. By the 19th century, cams had evolved into a highly advanced state, and they were used in lathes and other machine tools. However, cams couldn’t be abstractly programmed, which limited their applications.
Middle Ages
Moving forward, the late 20th century marked the beginning of what could be referred to as the Middle Ages in the history of CNC Routing. During this period, there was a shift from numerical control to computer numerical control (CNC). I can tell CNC machines were more sophisticated and capable compared to the earlier NC machines.
Present
Today, CNC routing has become an integral part of modern manufacturing. CNC routers can perform tasks of various carpentry shop machines such as the panel saw, spindle moulder, and boring machine. They also produce intricate designs for door carvings, decorations, and musical instruments.
3. Advantages of CNC Routing
With CNC routing, firms experience substantial benefits as compared to traditional manual routing. Listed below are the benefits to know about:
Precision and Accuracy
In any manufacturing environment, precision and accuracy are critical. At Suproto we have seen, CNC routing exhibits a high level of both. Traditional handheld routers, despite being versatile, are prone to human error. In contrast, CNC routers are governed by software that ensures exact routing parameters, which translates to more precise and accurate work.
Increased Efficiency and Productivity
Another undeniable benefit is the increase in efficiency and productivity. A CNC router can perform the same operation repeatedly with unerring accuracy and speed, making it an indispensable tool for mass production. For me, repeatability is also remarkable, with the machine capable of operating unattended for extended periods.
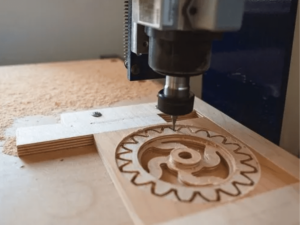
Cost-Effectiveness
CNC routing systems, despite their initial cost, prove to be cost-effective in the long run. I can speak truly of this: they reduce manpower costs as less personnel are needed to operate them compared to traditional routers. Additionally, their accuracy and speed mean that materials and time are used more efficiently, translating into cost savings.
4. Types of CNC Routers
CNC Routers are integral to various manufacturing processes. The classification of CNC routers is generally based on the number of axes they can manipulate. The more axes a CNC router has, the more complex the shapes it can produce. Here are some to explore:
3-Axis CNC Routers
3-axis CNC routers are the most basic type and are highly versatile. These routers move in three directions, namely X, Y, and Z axes. They are primarily used for parts that don’t require complex side milling or other sophisticated operations. Check them out at Suproto.
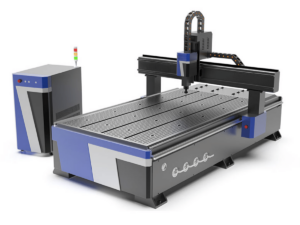
4-Axis CNC Routers
4-axis CNC routers add an additional axis of rotation compared to 3-axis models. This added complexity enables them to perform more intricate operations. For example, they can be used in the production of complex furniture parts or automotive components.
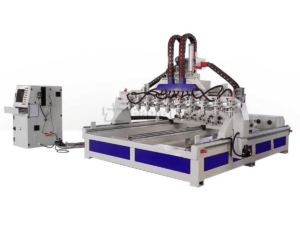
5-Axis CNC Routers
For the most demanding and complex operations, 5-axis CNC routers are often employed. These machines have five axes of movement and are capable of producing extremely intricate and precise parts. From my experience, aerospace and automotive industries often use 5-axis CNC routers to create components that require high precision and complex geometries.
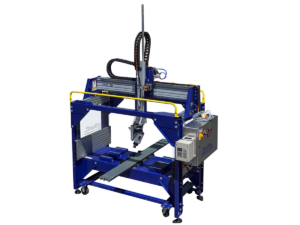
5. The Core Components of a CNC Router
To fully appreciate the capabilities of CNC routers, it is essential to understand their core components. These components work in unison to translate digital designs into physical parts with high precision and efficiency. Below are the ff:
The CNC Controller
The controller is essentially the brain of the CNC machine. From what I know, it is responsible for interpreting computer instructions and directing the driving system. According to VMR, the CNC Controller Market size is expected to develop revenue and exponential market growth at a remarkable CAGR during the forecast period from 2023–2030.
Drive System and Motors
The drive system comprises the elements that enable the machine to move along the axes (X, Y, Z) during cutting. It involves a combination of components including motors, lead or ball screws, and sometimes rack and pinions to convert controlled rotary motion to controlled linear motion, and this system is integral in determining the machine’s cutting speed, cutting force, precision, and accuracy.
Spindle
The spindle is the part that does the actual cutting by rotating its cutting bit at varying speeds. I can tell, it is critical for achieving the desired precision in the final product. According to Market Watch, the Global CNC Spindle market is anticipated to rise at a considerable rate during the forecast period, between 2022 and 2030.
Cutting Tools
Various cutting tools can be attached to the spindle, allowing the CNC router to perform a range of operations such as cutting, shaping, and engraving. For example, different CNC router bits are designed for specific geometries, and selecting the appropriate bit is crucial for the efficiency and success of the project.
6. Materials Suitable for CNC Routing
CNC routing isn’t just about machinery; the materials involved are equally critical. There’s a wide array of materials that can be effectively processed using CNC routing techniques. See the ff below:
Hard Materials: Wood, Metal, and Plastic
CNC routers can be used to cut designs on hard materials such as composites, plastics like acrylic and polycarbonate, and metals including aluminum. These materials are commonly used in industries such as construction, automotive, and product manufacturing.
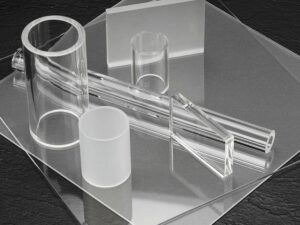
Soft Materials: Foam and Rubber
Transitioning from metals, CNC routers are also remarkably proficient at handling softer materials such as foams and synthetic rubbers. These materials find a plethora of applications ranging from packaging and insulation to seals in various industries. It’s exciting to know that the versatility of CNC routers extends beyond hard materials, making them invaluable assets in various production processes.
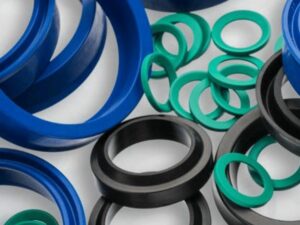
7. Safety Measures in CNC Routing
While CNC routing provides numerous benefits, it is vital that safety is given paramount importance during operations to protect both the operators and the machinery.
Basic Safety Rules
First things first, adhering to basic safety rules is a must. This includes ensuring that the machine is in top-notch condition, keeping the workspace spick and span, and religiously following the manufacturer’s guidelines. Clean machines not only have longer lifespans but also reduce the risks of cuts and burns
Protective Gear and Equipment
Don’t forget the armor! At Suproto, we make sure operators wear appropriate protective gear like safety glasses and ear protection. This protective gear is like a personal superhero outfit, shielding the body from potential hazards such as flying debris and noise.
Emergency Procedures
Now, being the proactive folks that we are, having well-practiced emergency procedures is the cherry on top. This ensures that in the case of an incident (knock on wood), the response is swift, effective, and minimizes harm to personnel and damage to equipment.
The following table outlines essential emergency procedures for CNC routing, providing swift and effective responses to incidents while prioritizing personnel safety and equipment protection.
Emergency Procedure |
Description |
Fire Emergency |
In case of a fire, immediately activate the fire alarm, evacuate the area, and notify the appropriate authorities. Do not attempt to extinguish the fire unless trained and equipped to do so safely. Follow established evacuation routes and assembly points. |
Medical Emergency |
If someone sustains an injury or requires medical attention, call emergency medical services (911) immediately. Administer first aid if trained to do so. Clear the area around the injured person and provide assistance until medical help arrives. |
Machine Malfunction |
If the CNC router malfunctions or exhibits unusual behavior, immediately stop the machine by activating the emergency stop button or switch. Isolate the power supply to prevent further operation. Report the issue to maintenance personnel and refrain from attempting repairs unless authorized. |
Power Failure |
In the event of a power outage or loss of electrical supply, ensure the CNC router is switched off. Safely secure loose materials, tools, and components to prevent accidents when power is restored. Follow company protocols regarding resuming operations after power is restored. |
Chemical Spill |
If a hazardous chemical is spilled during CNC routing, evacuate the area immediately and warn others in the vicinity. If safe to do so, contain the spill using appropriate absorbent materials and follow established procedures for chemical spill cleanup. Notify the appropriate personnel and provide necessary information about the spill. |
Personal Injury |
If an individual sustains a minor injury during CNC routing, such as a cut or abrasion, they should seek first aid or medical attention as necessary. Report the incident to the supervisor or designated safety personnel to ensure proper documentation and investigation. |
Emergency Evacuation |
In the event of a facility-wide emergency, follow evacuation procedures established by the company. Exit the building using designated evacuation routes and proceed to assembly points or safe areas. Do not re-enter the building unless authorized by emergency personnel. |
8. Challenges and Limitations of CNC Routing
While CNC routing has transformed manufacturing processes, it’s important to acknowledge the challenges and limitations associated with it. Here are some to consider:
Initial Setup and Maintenance Costs
Hold on to your wallets, folks! The initial investment in CNC routing machinery can be quite a punch. Additionally, maintenance costs can have its way breaking into the piggy bank, especially if specialized parts or servicing are needed.
Need for Technical Expertise
Operating a CNC router is not a walk in the park, it demands a certain level of technical expertise. Take note, no one wants just anyone fiddling with these machines. Proper training in basic operations and an understanding of the software and hardware are essential
Material Limitations
Speaking from experience, CNC can handle a wide range of materials, but there are limitations. Certain materials may not be compatible with CNC routing or may require specialized equipment and tooling, which could increase costs.
Dive Deeper Into Our Resources
Looking for more diverse services options? Browse through our handpicked selections:
For some insightful reads, we’ve curated a list of recommended articles just for you:
Still haven’t found what you’re looking for? Don’t hesitate to contact us. We’re available around the clock to assist you.
Conclusion
We have learned CNC routing is a versatile manufacturing process that utilizes computer-controlled cutters to carve materials with precision and accuracy. This technology has proven to be invaluable in various industries such as woodworking, metal fabrication, and plastics. Consider how CNC routing can enhance the productivity and profitability of the manufacturing business.
At this point, reach out to us for any queries or insights on integrating CNC routing into operations. By connecting with our experts, let’s unlock the potential of this innovative technology and edge ahead in the competitive market. Contact us today and let’s carve a path to success together!