According to data research on processing technology in related industries, laser cutting is the most important cutting technology in the laser processing industry, and its proportion can reach 70%, which shows that its application is extensive and important. Laser cutting technology is an important part of laser processing technology, and it is also one of the more advanced cutting technologies recognized in the world.
With the continuous development of social production and the continuous improvement of industrial processing technology, laser cutting technology is also developing and progressing rapidly.
1. Overview of Laser Cutting Machine and Its Related Principles
Laser
As a kind of coherent light, it has the advantages of excellent monochromatic performance, high brightness, high energy, and excellent directionality. It is widely used in laser cutting, drilling, welding and marking and many other aspects. At the same time has a large development space and development potential.
Laser Cutting Machine
It can be widely and widely used to cut many metal materials such as ordinary steel plate, hard alloy and stainless steel, as well as many non-metal materials such as ceramics, glass, and fiberboard. The operation system of laser cutting machine is mainly divided into three important parts: machine tool host, laser and control system.
As the central part of the entire system, the control system is in charge of and coordinates the normal work of the entire system. Its main task is to coordinate and control the trajectory of processing, control the position of the focus, and at the same time pay attention to the harmony with the machine, light, and electricity.
The Principle of Laser Cutting
The laser-cutting machine is capable of utilizing a focused laser beam with tremendous heat-generating power, reaching temperatures in the tens of thousands of degrees. This intense heat enables instant melting and evaporation of even the toughest materials, accompanied by a powerful shock wave that explosively removes molten material.
The laser-cutting process involves the following steps:
- Concentration of Laser Beam: The machine focuses the laser beam onto a specific point on the material’s surface. This concentration triggers the conversion of light energy into heat energy within microseconds.
- Rapid Temperature Increase: The temperature at the focal point rises rapidly, initially reaching the material’s melting point and then progressing to its boiling point.
- Material Gasification: As the temperature rises, the material transitions into a gaseous state, creating a small hole.
- Controlled Laser Beam Path: The laser beam follows a predetermined path under the control and operation of the laser cutting machine.
Throughout the entire process, the material’s surface undergoes continuous liquefaction and gasification. This results in the formation of a slender and elongated slit that aligns with the laser’s trajectory.
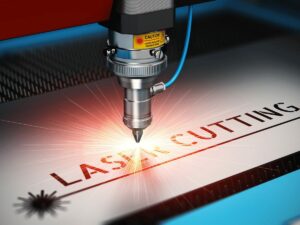
2. Advantages of Laser Cutting Technology
Laser-cutting technology has brought about a revolution in sheet metal fabrication, providing a multitude of advantages that significantly improve efficiency and precision. Some advantages of laser cutting technology are as follows:
- Fast Cutting Speed: Laser cutting technology offers exceptional cutting speed, significantly enhancing production efficiency. By harnessing the power of laser beams, it enables swift and precise cuts, accelerating manufacturing processes.
- Small Slit and Neat Incisions: Laser cutting achieves meticulous precision with its ability to create small, smooth slits and precise incisions. This exceptional level of precision guarantees the delivery of high-quality results every time.
- Minimal Tool Wear: Laser cutting technology stands apart from traditional cutting methods by minimizing tool wear, leading to reduced maintenance and replacement expenses. This advantage not only enhances cost-effectiveness but also ensures consistent cutting performance over extended periods.
- Limited Heat Range: Laser-cutting technology excels in focusing heat on a precise area, thereby minimizing the heat-affected zone on the cutting surface. This targeted heat application ensures minimal distortion or damage to the surrounding material, resulting in clean and precise cuts.
- Versatility: Laser cutting is highly versatile, allowing the processing of various shapes without limitations, making it easier to achieve precise numerical control.
- Mold-Free Processing: Laser cutting technology eliminates the reliance on molds, offering the versatility to accomplish various sheet metal processing tasks with exceptional precision and quality. With this mold-free approach, manufacturers can swiftly adapt to changing design requirements and produce intricate and customized metal components efficiently.
- Increasing Industrial Adoption: Industrial manufacturing units are wholeheartedly embracing laser cutting technology in sheet metal processing, fully aware of its pivotal role and the array of advantages it brings. By adopting laser cutting technology, these units unlock enhanced productivity, superior precision, and cost-efficiency, propelling their manufacturing operations to new heights.
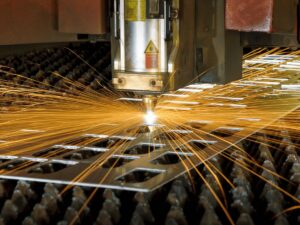
3. The Development and Status Quo of Laser Cutting Technology
In my country’s industrial processing system, laser technology is mainly used in cutting, welding, marking, and heat treatment. Although the start of my country’s laser cutting industry is not much later than that of Western countries, due to its poor foundation, laser processing technology has not yet been widely used, and the overall development level of the laser processing industry is still far from that of advanced countries.
Laser cutting technology is widely used and continually evolving in various industries. With the rapid development of my country’s economy and technology, there is a growing need for sheet metal processing and the establishment of processing technology centers in industrial cities to boost economic benefits.
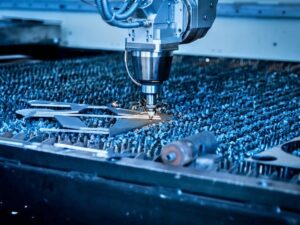
4. Practical Application and Advantages of Laser Cutting Machine in Sheet Metal Processing
Improve Efficiency
Laser cutting maximizes the benefits of programming software, significantly increasing the utilization rate of thin plate materials while minimizing material waste. This approach simultaneously reduces labor intensity and worker strain, achieving desired outcomes. Optimized nesting in laser cutting minimizes material clamping and processing time, improving efficiency and material savings.
Shorten the Development Cycle
Laser cutting machines drive product development by saving time and reducing the need for molds. They enhance production efficiency, ensure high-quality parts, and facilitate small batch production. Laser cutting also enables precise size positioning, paving the way for future mass production in a rapidly evolving market environment.
Cost Reduction
Laser cutting machines streamline sheet metal processing, allowing for one-time forming and direct welding of plates. This reduces the process and construction period, enhances work efficiency, and optimizes labor intensity and processing costs. Additionally, it promotes a better working environment, accelerates research and development, reduces mold investment, and effectively cuts costs.
This table outlines various factors impacted by laser cutting technology, highlighting its potential to enhance work efficiency, optimize labor intensity, and effectively cut costs.
Cost Reduction Factors |
Impact on Cost Reduction |
One-time forming and direct welding of plates |
Reduces process and construction period, minimizing material waste and labor costs. |
Enhanced work efficiency |
Increases productivity, leading to reduced labor expenses and faster project completion. |
Optimization of labor intensity |
Reduces the need for manual labor, saving on workforce-related expenses. |
Improved working environment |
Potential cost savings due to better safety and reduced worker downtime. |
Accelerated research and development |
Shortens development cycles, leading to quicker product releases and cost savings. |
Reduced mold investment |
Eliminates the need for expensive molds, reducing upfront capital expenditure. |
Effective cutting costs |
Lower material costs due to optimized material usage and minimal wastage. |
Improve Labor Productivity
Laser cutting machines in sheet metal processing significantly reduce product manufacturing cycles and mold investments. They enhance worker processing speed, eliminate unnecessary steps, and efficiently process complex parts with improved accuracy. This improves productivity by shortening processing cycles, enhancing accuracy, and eliminating the need for stamping die replacements.
Dive Deeper Into Our Resources
Looking for more diverse service options? Browse through our handpicked selections:
For some insightful reads, we’ve curated a list of recommended articles just for you:
Still haven’t found what you’re looking for? Don’t hesitate to contact us. We’re available around the clock to assist you.
5. Conclusion
In short, laser cutting machines have been well and widely used in many fields, especially in sheet metal processing as a new technical process, laser cutting has greatly improved production efficiency and product quality. In the future, laser-cutting technology will definitely gain more affirmation in production and life, and its application and development prospects are very broad.
With the continuous development of social industry and the advancement of laser processing technology, laser cutting technology will inevitably become an important processing method in the application of sheet metal processing technology. Therefore, it is worthy of the attention and attention of the majority of peers and vigorously promoted in actual production.