Caught in the titanium vs. aluminum standoff, trying to choose the best material for a business project? Titanium and Aluminum are really two frontrunners. However, because of their shared silvery hues and widespread applications make it harder to decide for some businesses.
Each metal has its own set of impressive properties: Titanium excels in strength and high-temperature corrosion resistance, while Aluminum outperforms in thermal conductivity and cost-effectiveness. Through this blog post, let me unveil more about the two.
So buckle up, and let’s start this metallic journey!
1. Importance of Metal Selection in Various Industries
Metals have been an integral part of human civilization since antiquity, and their importance has only escalated with the evolution of industries. The importance of metal selection in various industries cannot be overstated. Each metal has unique properties that make it apt for certain applications.
I have seen in the aerospace industry, for example, requires metals that are lightweight and have high tensile strength, while the automotive industry may prioritize durability and resistance to corrosion. On the other hand, the medical industry requires materials that are biocompatible and non-reactive.
2. In-Depth Exploration of Titanium
Let’s dive into the intricate details of titanium’s alloys, production processes, and innovations as we unravel its elemental secrets and understand why it’s hailed as the metal of choice for applications demanding both strength and lightness.
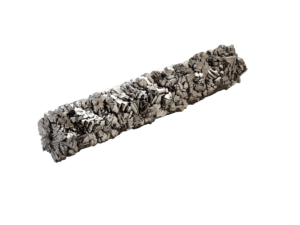
Elemental Properties and Characteristics
Diving into the physical properties of titanium, it’s a lightweight, strong, and rust-resistant silver-white metal. In its pure form, titanium is relatively soft. However, when alloyed, it becomes incredibly strong – even stronger than steel and aluminum. It also has a high melting point, and its density is about 4.5 g/cm3. These characteristics make it ideal for applications that require strength without the burden of weight.
As for the chemical properties, titanium is known for its strong affinity for oxygen. This property implies that conventional titanium metal production processes are energy-intensive. Moreover, titanium is non-toxic and has a high resistance to corrosion, which makes it an excellent choice for applications exposed to harsh environments.
Manufacturing Process of Titanium
The production of titanium has historically been an expensive and energy-consuming process. Manufacturers like Suproto and others have been exploring alternative production methods that are more energy-efficient and cost-effective. See below the ff:
- Step#1 Extracting the Raw Material
Titanium is sourced from minerals like rutile and ilmenite. These minerals are found in sands and rocks. The traditional method to extract titanium involves a smelter containing chlorine gas and a carbon-based reducer, known as coke, with temperatures of around 1,000 degrees Celsius producing titanium tetrachloride and carbon dioxide as a by-product.
- Step#2 Refining and Purification
Once extracted, titanium goes through various refining processes. It is purified by removing impurities like iron and magnesium. During the Kroll process, titanium tetrachloride is subjected to a high-temperature treatment with magnesium to release pure titanium metal as porous structures called sponges.
- Step#3 Forming the Titanium Alloy
Titanium is often mixed with metals like aluminum and vanadium. The mixture results in titanium alloys that have outstanding properties, like the alpha/beta titanium alloys. Notably, titanium’s high strength, low weight, and high corrosion resistance make it ideal for applications like architectural buildings and aerospace where strength and lightness are paramount.
- Step#4 Rolling and Shaping
The titanium alloys are then rolled into sheets or bars. This is a meticulous process as the titanium must be shaped into precise forms for various applications. For example, thin sheets are essential for aircraft bodies. Additionally, the forming process ensures the structural integrity and dimensions are maintained for specific applications such as in aerospace, medical implants, and construction.
- Step#5 Heat Treatment and Finishing
Heat treatment helps in achieving desired mechanical properties. Afterward, titanium goes through finishing processes to improve its surface quality, making it suitable for specialized applications like in aircraft and medical devices.
- Step#6 Quality Checks and Shipment
Before the titanium leaves the manufacturing plant, it goes through strict quality checks. Ensuring that only the best product reaches the customer is vital, especially when the titanium is used in high-stakes industries like aerospace.
Key Applications of Titanium
The aerospace and defense industries have been key beneficiaries of titanium’s outstanding properties. Due to its high strength-to-weight ratio and resistance to corrosion, it’s used extensively in military aircraft such as the F-22 and UH-60 Black Hawk helicopters. Additionally, as space exploration advances, titanium is expected to play an even greater role in the construction of spacecraft.
Transitioning to the medical field, titanium, and its alloys are pivotal for medical implants due to their biocompatibility and strength. Beta-titanium alloys, in particular, have found favor in the biomedical industry because their reduced modulus compared to human bone makes them ideal for orthopedic implants.
As a sports enthusiast myself, I have seen titanium’s strength and lightweight properties have made it a popular choice for sports equipment. From golf clubs to tennis rackets, the use of titanium ensures high performance and durability without the equipment being heavy or cumbersome.
3. Aluminum: A Closer Look
Let’s step into the versatile world of aluminum, an essential element known for its lightweight characteristics, conductivity, and resistance to corrosion. Here is an insightful glimpse into the metallurgy, applications, and innovations that have positioned aluminum as a cornerstone material in industries.
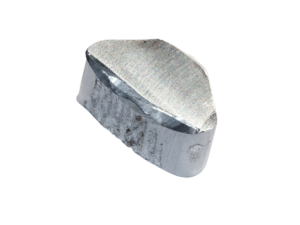
Elemental Properties and Characteristics
Aluminum is renowned for its lightness, with a density of approximately one-third that of steel. I believe, this light metal also boasts impressive strength, especially when alloyed with small amounts of other metals. Aluminum is ductile, making it easy to form into various shapes, and has high thermal and electrical conductivity.
Chemically, aluminum is highly reactive. It forms a thin, protective oxide layer when exposed to air, which prevents further oxidation and makes it resistant to corrosion. It’s also non-magnetic and non-toxic, which expands its array of applications.
Manufacturing Process of Aluminum
I am convinced that the process of manufacturing aluminum is a meticulously designed multi-step procedure. Let us discuss these 6 steps:
To manufacture aluminum, the first step is to mine bauxite. Bauxite is a rock rich in aluminum oxide. Large machinery is used to extract the ore from the earth. Once the bauxite is mined, it is then sent to processing plants to be converted into alumina, which is a powdery substance.
Alumina refining is the second step in aluminum production. This process involves treating the bauxite with chemicals to produce aluminum oxide. The Bayer process is one common method used, wherein bauxite is heated with an alkali mixture to yield alumina.
- Step#3 Electrometallurgical Processing
Electrometallurgical processing, famously known as the Hall-Héroult process, involves the electrolytic reduction of aluminum oxide to produce aluminum. This step requires a lot of electricity. Essentially, aluminum oxide is dissolved in molten cryolite, and an electric current is passed through, causing aluminum metal to form at the bottom of the tank.
Casting is one of the ways aluminum is shaped into products. Molten aluminum is poured into molds that duplicate the desired pattern. Techniques like die casting, permanent mold casting, and sand casting are the three most important methods to shape aluminum. These methods vary in speed, strength, and suitability for different product types.
Extrusion is a technique where a solid cylinder of aluminum is forced through a die opening by compression, essentially shaping it. This process can be highly customized by adjusting factors like the die design, billet temperature, and extrusion speed. Extrusion is popular for its near-limitless design possibilities and is used in manufacturing and construction applications.
- Step#6 Secondary Production
Secondary aluminum production is the process of making new aluminum from recycled scrap. This is an eco-friendly alternative and can produce high-quality aluminum. This method is especially popular for products like cans. Secondary production is a testament to the industry’s commitment to sustainability and resource efficiency.
Key Applications of Aluminum
- Aerospace and Transportation
Transitioning into applications, let’s start with the aerospace and transportation sectors. Aluminum’s high strength-to-weight ratio, corrosion resistance, and ease of fabrication make it an indispensable material in aircraft manufacturing. Its use isn’t just limited to planes; aluminum is also essential in the automotive industry, where it’s used to manufacture lightweight car bodies and components, reducing fuel consumption.
From aerospace, let’s delve into the everyday life of aluminum. It’s ubiquitous in the packaging industry, particularly in the form of beverage cans and foils. Personally, thanks to its ability to form a barrier to light, oxygen, moisture, and bacteria, because aluminum is an excellent material for food preservation. Moreover, in households, aluminum is the go-to material for utensils and cookware.
- Construction and Architecture
Now let’s build upon aluminum’s role in construction and architecture. Here, aluminum is prized for its strength, lightness, and resistance to corrosion. Whether it’s the dramatic sweeping curves of the Guggenheim Museum in Bilbao or the innovative designs by Suproto in China, aluminum has paved the way for modern, breathtaking structures.
4. Point-by-Point Comparison: Titanium vs Aluminum
At first glance, titanium and aluminum may seem similar, but upon closer inspection, they present some distinct differences. Titanium, often dubbed the “space-age metal,” is known for its incredible strength and durability, and is as strong as steel but with roughly half the weight. Aluminum, on the other hand, is the third most abundant element in the Earth’s crust and is renowned for its lightness and corrosion resistance.
Titanium’s excellent strength-to-weight ratio has made it a material of choice in aerospace engineering. Aluminum’s wide range of applications spans from aerospace, similar to titanium, to everyday items such as cans and foils. For me, titanium is biocompatible, making it invaluable in the medical field for surgical implements and implants. Aluminum’s conductivity and malleability make it ideal for electrical applications.
5. 5 Factors to Consider When Choosing Between Titanium and Aluminum
According to Statista, a total of approximately 9.5 million metric tons of titanium minerals were produced globally in 2022. While Aluminum is one of the world’s most abundant metals, typically extracted from bauxite ore. Making an informed decision requires a grasp of the subtle differences between the two metals. We shall examine 5 important variables when choosing between titanium and aluminum for various needs.
#1 Cost Considerations
Embarking on the financial aspect, it’s essential to know that titanium typically has a higher cost than aluminum. This is due to the more complex extraction process and its relatively lower abundance. In my point of view, in projects where budget is a significant constraint, aluminum might be the more economical choice.
The table below provides insights into the cost considerations between titanium and aluminum, highlighting the higher cost of titanium due to its complex extraction process and lower abundance. Explore how aluminum emerges as a more economical choice, making it a preferred option in projects where budget constraints play a significant role.
Cost Considerations: Titanium vs. Aluminum |
Description |
Higher Cost of Titanium |
Titanium generally has a higher cost compared to aluminum. This is primarily attributed to the more complex extraction process and the relatively lower abundance of titanium compared to aluminum. The higher cost of titanium makes it a less economically viable option, especially in projects where budget constraints play a significant role. |
Aluminum as a More Economical Choice |
Aluminum, on the other hand, is often considered a more economical choice due to its lower cost compared to titanium. Aluminum is more abundant and has a simpler extraction process, resulting in a more cost-effective production. This makes aluminum a preferred option in projects where budget considerations are crucial and cost optimization is a priority. |
#2 Strength and Durability Requirements
Flexing their muscles, let’s consider strength and durability. Titanium stands out here as it is significantly stronger and more durable than aluminum. This makes it an ideal choice for applications that demand high strength, for example, aircraft frames or surgical instruments.
#3 Weight Limitations
Lightening the load, if weight is a critical factor in the application, aluminum might edge ahead. Though titanium has a higher strength-to-weight ratio, aluminum itself is lighter, which can be an advantage in applications like automotive parts or consumer electronics where overall weight reduction is a goal.
#4 Corrosion Resistance Needs
Moving smoothly to corrosion resistance, both metals excel, but titanium takes the cake. Speaking from experience, Titanium’s ability to withstand harsh environments makes it an excellent choice for applications such as underwater or chemical processing equipment.
#5 Thermal and Electrical Conductivity Needs
As we reach the end of this metallic tale, it’s worth discussing thermal and electrical conductivity. Aluminum is the clear winner in this category, with excellent electrical and thermal conductivity, making it the material of choice for applications such as electrical wiring or heat sinks. While for the structural aspects where strength is paramount, titanium would be the material of choice. Check it out at Suproto.
Dive Deeper Into Our Resources
Looking for more diverse service options? Browse through our handpicked selections:
For some insightful reads, we’ve curated a list of recommended articles just for you:
Still haven’t found what you’re looking for? Don’t hesitate to contact us. We’re available around the clock to assist you.
Conclusion
In our exploration of Titanium Vs Aluminum, the complexities, and characteristics of these two remarkable metals have been unraveled. This analysis is of utmost importance when it comes to product design, especially for those involved in business industries. Is there a particular metal that could revolutionize product lines or manufacturing processes in your business?
The invitation is extended to reach out. Our team is here to assist businesses in making informed decisions that best align with their project requirements and objectives. Knowledge is the key to innovation, and communication is the key to understanding. Looking forward to being a part of the journey. Contact us today!