Ever found yourself asking, “What exactly is Wire EDM, and how does it work?” Creating complex and intricate components while maintaining high standards of accuracy and efficiency poses a significant challenge for manufacturers. That’s where Wire Electrical Discharge Machining (Wire EDM) comes into play.
Wire Electrical Discharge Machining is a machining process that utilizes electrical discharges to cut through various materials with incredible accuracy. It’s a technology that’s revolutionized manufacturing, making it possible to create complex shapes and intricate designs with unparalleled precision.
Read on and brace yourself for an enlightening exploration into the realm of Wire EDM, a technology that is set to revolutionize the production processes.
1. An Overview of Wire EDM
Wire Electrical Discharge Machining, or Wire EDM for short, is a transformative machining technique that cuts through hardened materials with the help of a thin, electrically charged wire used as an electrode. According to IQS Directory, wire electrical discharge machining (EDM) can machine parts resistant to conventional machining methods as long as they are electrically conductive.
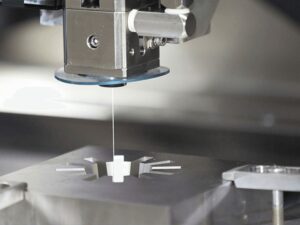
2. The History and Evolution of Wire EDM
Wire EDM has a rich history dating back to the turbulent times of World War II. Below, grasping its historical context can provide profound insights into the breadth of its current and potential applications.
The Birth of Wire EDM: 1940s
The 1940s marked the birth of Wire EDM, where Soviet scientists, in a bid to discover efficient ways to machine tough materials, stumbled upon the potential of electrical discharges. This marked the genesis of Wire EDM, an innovation that would change the face of machining.
Progression of Wire EDM: From the 1950s to the 1980s
Wire EDM technology experienced rapid development during the mid-20th century. With the basic principles firmly established, wire EDM’s focus shifted towards refining and enhancing technology, ultimately aiming to make it more accurate, reliable, and user-friendly.
The Modern Era of Wire EDM: 1990s to Today
The last few decades, starting from the 1990s, have seen Wire EDM evolve into a fundamental component of modern manufacturing. Anyone will agree that the dawn of the digital age led to the incorporation of computer technology into Wire EDM, resulting in the high-speed, automated machines that are ubiquitous in today’s industries.
3. How Wire EDM Works?
While Wire EDM technology may seem complex, the fundamental principles behind it are quite straightforward. It’s a process of controlled material removal, guided by a programmable control system and powered by electrical discharges. Let’s dive into the specifics.
Electrical Discharge Erosion
The cornerstone of the Wire EDM process is electrical discharge erosion. When the wire electrode is brought close to the workpiece, the power supply generates electrical discharges. These discharges pass through the dielectric fluid, which acts as a medium, causing localized melting and vaporization on the workpiece. As a result, material is gradually eroded, allowing the machine to achieve the desired shape.
Role of Dielectric Fluid
The dielectric fluid plays a critical role in the Wire EDM process. Not only does it serve as a medium for electrical discharges, but it also helps cool the workpiece and wire electrode, preserving their structural integrity. According to Engineering.com, it is even discovered that the erosion of electrical contacts could be controlled by immersing them in a dielectric fluid.
Programmed Path and Control System
Wire EDM machine uses a computer-aided control system to guide the wire along a programmed path. The path is typically defined using CAD/CAM software, allowing the machine to achieve intricate geometries and complex shapes with precision. Amazingly, the control system continuously adjusts the wire’s position and the power supply, ensuring the cut stays on track and meets the specified tolerances.
4. Benefits of Using Wire EDM
The unique machining process of Wire EDM delivers a host of advantages, making it an integral part of many industrial operations. Here let’s talk about wire EDM’s benefits that cater to a wide array of manufacturing needs:
Precision and Accuracy
One of the most compelling advantages of Wire EDM is its ability to deliver exceptional precision and accuracy. By controlling the electrical discharges between the wire electrode and the workpiece, Wire EDM achieves intricate and detailed cuts. This capability allows for the creation of complex geometries and designs, ensuring adherence to exact specifications and tight tolerances.
Flexibility with Materials and Shapes
Another significant benefit of Wire EDM is its incredible flexibility in dealing with a wide variety of materials and shapes. It’s capable of cutting through hardened metals, such as tool steel and titanium, which typically require pre-heat treatment in traditional machining. Moreover, the nature of the wire-guided process allows for intricate shapes, undercuts, and sharp internal corners, providing unparalleled design freedom.
The following table illustrates the remarkable flexibility of Wire EDM in handling a diverse range of materials and shapes, offering advantages such as cutting hardened metals and enabling intricate designs with sharp internal corners.
Material |
Capability |
Hardened Metals (e.g., tool steel, titanium) |
Wire EDM can cut through hardened metals without the need for pre-heat treatment, unlike traditional machining methods. |
Soft Metals (e.g., aluminum, copper) |
Wire EDM can effectively work with soft metals, allowing for precise cutting and shaping. |
Exotic Alloys (e.g., Inconel, Hastelloy) |
Wire EDM is capable of handling exotic alloys, providing versatility in machining applications. |
Conductive Materials (e.g., brass, bronze) |
Wire EDM can cut through various conductive materials with ease, making it suitable for a wide range of applications. |
Non-Conductive Materials (e.g., ceramics, composites) |
Although Wire EDM is primarily used for conductive materials, specialized techniques like dielectric fluid flushing allow it to work with some non-conductive materials. |
Complex Shapes and Intricate Designs |
Wire EDM’s wire-guided process enables the creation of intricate shapes, undercuts, and sharp internal corners, offering unparalleled design freedom. |
Tight Tolerances |
Wire EDM is capable of achieving high precision and tight tolerances, ensuring accuracy in the final product. |
Thin and Delicate Materials |
Wire EDM can work with thin and delicate materials without causing distortion or damage, making it suitable for intricate work. |
Reduced Stress on the Workpiece
The non-contact nature of the Wire EDM process is a blessing when it comes to preserving the integrity of the workpiece. Unlike traditional machining techniques, Wire EDM does not exert mechanical force on the workpiece, thereby eliminating the risk of deformation or damage. At Suproto, this feature is particularly useful when working with delicate or brittle materials.
5. Types of Wire EDM Machines
Wire EDM technology has evolved into several types of machines, each tailored to specific needs and applications. Here are some types of wire EDM machines:
Conventional Wire EDM Machines
Conventional Wire EDM machines form the bedrock of this technology. Believe me, while they may not possess the rapid cutting speeds of their high-speed counterparts, they offer exceptional precision and consistency. These machines are typically used in the production of intricate parts that require stringent tolerances, making them a staple in many industries.
Small Hole EDM Drilling Machines
Small hole EDM drilling machines are a specialized variation of Wire EDM technology. For instance, these machines are uniquely designed to create small, precise, and deep holes in hardened materials. This capability provides a viable alternative in scenarios where traditional drilling methods struggle, particularly when high aspect ratio holes are needed in hard or brittle materials.
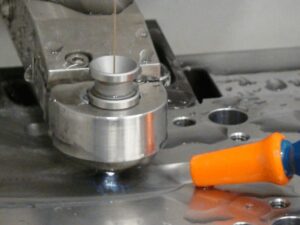
High-Speed Wire EDM Machines
As the name suggests, high-speed Wire EDM machines offer significantly faster cutting speeds compared to conventional Wire EDM machines. While they maintain excellent precision, their primary advantage lies in their ability to drastically reduce machining times, thereby increasing productivity. This feature makes high-speed Wire EDM machines particularly useful for large production runs and industries.
6. The Key Components of a Wire EDM Machine
A Wire EDM machine is a marvel of engineering, composed of several key components that work in unison to deliver high-precision machining. Understanding the components below will shed light on how to maximize its efficiency and effectiveness:
The Power Supply and Control System
At the helm of a Wire EDM machine, you’ll find the power supply and control system. The power supply governs the electrical discharges that erode the workpiece, ensuring that they occur at the right moment and with the correct intensity. The control system, on the other hand, meticulously orchestrates the movement of the wire electrode and workpiece.
The Wire Feed System
The wire feed system of a Wire EDM machine serves a crucial role. It is responsible for guiding the wire electrode through the process, maintaining appropriate tension and speed. Trust me, this system ensures the smooth and accurate travel of the wire through the workpiece, directly influencing the quality of the cut.
The Work Tank and Dielectric System
The work tank and the dielectric system play a joint role in the Wire EDM process. The work tank is the stage where the action takes place; it’s where the workpiece and wire electrode come together. The dielectric system involves the dielectric fluid that fills the work tank. This fluid plays a dual role: it acts as an insulator until a high enough voltage is applied to initiate the electrical discharges.
The Positioning System
At Suproto, the positioning system of a Wire EDM machine is the component that ensures the precise alignment and movement of the workpiece and wire electrode. This system, usually controlled by computer-aided design and manufacturing software (CAD/CAM), enables the machine to make precise cuts following complex geometrical paths.
7. Wire EDM Operation: Step by Step
Operating a Wire EDM machine involves a series of steps that require both technical knowledge and hands-on skills. Here are the steps on how a wire EDM machine works:
Step#1 Preparing the Wire EDM Machine
The first step of operating a Wire EDM machine is preparation. This step involves several tasks, including programming the control system with the desired path and cutting parameters, selecting and loading the wire electrode, and ensuring the dielectric fluid is at the appropriate level. These initial tasks set the stage for a successful machining operation.
Step#2 Wire Threading and Setup
Following the machine’s preparation, the next stage is wire threading and setup. This step involves feeding the wire through the guide system to the starting point on the workpiece. Precision is critical here as any misalignment can affect the accuracy of the cut. The wire must be accurately positioned, and its tension and feed speed are set to appropriate levels as per the cutting parameters.
Step#3 Cutting Process
The cutting process is where the magic happens. Guided by the control system, the wire starts to move along the programmed path. As it does, the power supply initiates the electrical discharges between the wire and the workpiece, with the dielectric fluid acting as a medium. This controlled sparking erodes the material, effectively cutting the workpiece.
Step#4 Post-Processing and Finishing
After the machine has completed the cut, the process moves into the post-processing stage. The cut workpiece is removed from the work tank, thoroughly cleaned, and inspected for quality and accuracy. The machine, too, undergoes maintenance tasks, including cleaning the work tank and replenishing the dielectric fluid if necessary.
8. Common Applications of Wire EDM
Wire EDM technology, with its unique capabilities, finds applications in various industries. Here are some of the sectors where wire EDM proves to be useful:
Aerospace Industry
In the aerospace industry, where precision, reliability, and material integrity are critical, Wire EDM proves to be an invaluable tool. The technology is used to manufacture various components, such as turbine blades, fuel system components, and other intricate parts made from high-strength, temperature-resistant alloys.
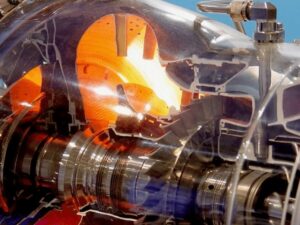
Automobile Manufacturing
The automotive industry also benefits greatly from Wire EDM technology. The process is used in the production of components like engine parts, gears, and transmission components. In my opinion, wire EDM’s ability to work with hardened materials and create complex shapes with tight tolerances makes it an ideal solution for high-performance automotive applications.
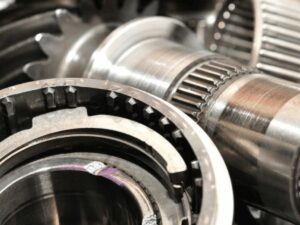
Medical Device Production
Medical device production, another field where precision and material versatility is key, often turns to Wire EDM for the manufacturing of critical components. For example, surgical instruments, orthopedic implants, and other specialized devices are often made from biocompatible metals. This ability to create intricate features and its compatibility with a wide range of materials make it well-suited to this highly specialized field.
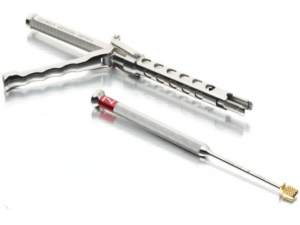
Dive Deeper Into Our Resources
Looking for more diverse service options? Browse through our handpicked selections:
Still haven’t found what you’re looking for? Don’t hesitate to
contact us. We’re available around the clock to assist you.
Conclusion
Anyone will agree that wire EDM is a highly versatile and precise machining technology that plays a critical role in numerous industries. From its rich history and working principle to the benefits it offers and its varied applications, understanding Wire EDM can open up new possibilities in manufacturing.
Looking for a business partner to consider incorporating Wire EDM into the manufacturing process? Suproto, a leading manufacturer of Wire EDM machines, is ready to help. Our team of experts can provide advice tailored to the specific needs, helping it optimize the operations and reach the production goals. Contact us to learn more about how Wire EDM can revolutionize the manufacturing process.