Ever struggled to make sense of the differences between 5052 and 6061 aluminum alloys? Both offer distinctive features, but which one is the optimal choice for manufacturing endeavors? Add to that, the high-stakes nature of material selection in manufacturing, which directly impacts product quality, durability, and cost-efficiency.
This blog post aims to cut through the complexity and provide a detailed, comprehensive guide to these popular alloys.
Read on to dive into the intricate world of aluminum alloys.
1. Understanding Aluminum Alloys
Aluminum alloys hold a paramount position in a myriad of industrial applications, offering a fascinating blend of versatility and strength. Here, we’ll take a look at the aluminum alloys’ universe, their inherent characteristics, classification, formation, and their impact on different industries:
The Science Behind Aluminum Alloys
An aluminum alloy is a composite material, essentially an amalgamation of aluminum, the base metal, and a variety of other elements. These additional constituents can range from silicon, magnesium, copper, to zinc, each playing a unique role in enhancing the base metal’s properties.
Classification of Aluminum Alloys
Broadly, aluminum alloys fall into two categories: heat-treatable and non-heat-treatable. Heat-treatable alloys, as the name implies, gain significant strength from heat-treatment processes such as solution heat treatment and aging. On the other hand, non-heat-treatable alloys derive their strength from cold working or strain hardening.
Formation of Aluminum Alloys
Believe me, creating an aluminum alloy is a meticulous process, involving precise measurements, controlled environments, and often, sophisticated machinery. The process begins with molten aluminum, into which the alloying elements are introduced. The resultant mix is then cooled and subsequently rolled into the desired thickness.
Role of Aluminum Alloys in Different Industries
Aluminum alloys have become indispensable in a multitude of industries due to their exceptional characteristics. They are omnipresent in the automotive industry, owing to their lightweight and strength, leading to fuel efficiency. The aerospace industry heavily relies on these alloys for aircraft structures due to their strength-to-weight ratio and corrosion resistance.
2. In-Depth Look at 5052 Aluminum Alloy
Now that we have a clear understanding of aluminum alloys, let’s zoom in on one of the prominent members of the non-heat-treatable family – the 5052 aluminum alloy. Below let us recognize 5052’s strength, corrosion resistance, and excellent formability:
Composition and Properties of 5052
The 5052 alloy composition is a precise mixture of aluminum (95.7% – 97.5%), chromium (0.15% – 0.35%), and magnesium (2.2% – 2.8%). The prevalence of magnesium adds to the alloy’s strength, while chromium enhances its resistance to corrosion. According to Thomas Net, the properties of 5052 aluminum alloy differ based on how it is cold worked, or made stronger using the work-hardening process.
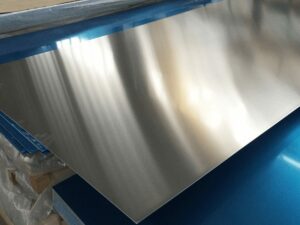
Manufacturing Process of 5052
At Suproto, the manufacturing process of 5052 aluminum alloy involves several precise steps to ensure the desired composition and properties of the alloy are achieved. Let’s explore the step-by-step process of manufacturing 5052 aluminum alloy.
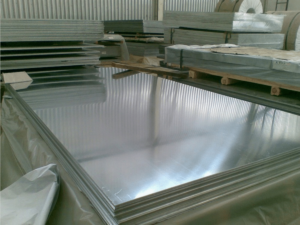
Step#1 Raw Material Preparation and Alloy Design
The first step in the manufacturing process of 5052 aluminum alloy involves sourcing and preparing the raw materials. Aluminum, the primary component of the alloy, is extracted from bauxite ore through a process called the Bayer process. The extracted aluminum is then refined and purified to remove impurities.
Step#2 Melting and Casting
The next step is the melting and casting of the prepared aluminum alloy. The pure aluminum and the alloying elements are carefully weighed and mixed together in precise proportions. The mixture is then melted in a furnace at high temperatures until it reaches a liquid state.
Step#3 Hot and Cold Rolling
After the casting process, the 5052 aluminum alloy goes through a series of rolling operations to achieve the desired thickness and mechanical properties. The first step is hot rolling, where the alloy is passed through a set of heated rollers. This process helps in reducing the thickness and refining the microstructure of the alloy.
Main Uses and Applications
5052 aluminum alloy, renowned for its exceptional corrosion resistance, formability, and versatility, finds widespread use across numerous industries. Let’s explore some of the common uses and applications of 5052 aluminum alloy.
Marine and Naval Applications
The marine industry extensively utilizes 5052 aluminum alloy due to its superior resistance to corrosion in saltwater environments. It is commonly employed in the construction of boat hulls, decks, and other components exposed to the harsh marine conditions. Additionally, 5052 alloy is used for marine fuel tanks, piping systems, and other critical parts where resistance to saltwater corrosion is vital.
Automotive Industry
5052 aluminum alloy plays a vital role in the automotive sector, thanks to its lightweight nature, high formability, and corrosion resistance. It finds application in the manufacturing of vehicle panels, body structures, and other components, contributing to weight reduction and improved fuel efficiency.
Architectural and Construction Sector
In the field of architecture and construction, 5052 aluminum alloy offers a winning combination of aesthetics, durability, and resistance to harsh weather conditions. It is frequently utilized in the fabrication of architectural panels, roofing systems, window frames, and facades. The alloy’s formability allows for creative and intricate designs, while its corrosion resistance ensures longevity and low maintenance requirements.
Strengths and Weaknesses of 5052 Aluminum Alloy
5052 aluminum alloy possesses several notable strengths that contribute to its popularity in various industries. However, like any material, it also has a few weaknesses to consider. Let’s explore the strengths and weaknesses of 5052 aluminum alloy.
Strengths:
- One of the key strengths of 5052 aluminum alloy is its exceptional resistance to corrosion.
- 5052 aluminum alloy offers excellent formability, allowing it to be easily shaped, bent, or formed into complex structures without compromising its mechanical properties.
- Despite its impressive formability, 5052 aluminum alloy also exhibits good strength characteristics. It provides sufficient strength for many structural applications without being overly heavy or cumbersome.
Weaknesses:
- While 5052 aluminum alloy is generally considered weldable, it may present challenges in certain welding applications. The alloy has a tendency to develop welding defects such as porosity if not properly controlled.
- Unlike some other aluminum alloys, 5052 is not heat-treatable. It cannot be significantly strengthened through heat treatment processes.
3. In-Depth Look at 6061 Aluminum Alloy
Shifting our focus now to 6061, a popular heat-treatable alloy. Here let’s see why the 6061 aluminum alloy has garnered significant recognition in fields that demand structural durability and versatility.
Composition and Properties of 6061
6061 is a result of a precise concoction that comprises of aluminum (95.85% – 98.56%), paired with other elements including magnesium (0.60% – 1.2%), silicon (0.4% – 0.8%), and trace amounts of chromium. Accoding to Mat Web, 6061 combines relatively high strength, good workability, and high resistance to corrosion; and is widely available.
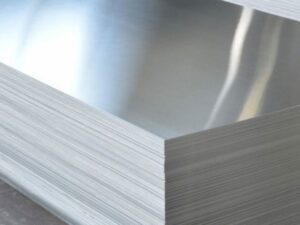
Manufacturing Process of 6061
The manufacturing process of 6061 aluminum alloy involves several steps to ensure the desired composition, properties, and structural integrity of the alloy are achieved. Let’s explore the step-by-step process of manufacturing 6061 aluminum alloy.
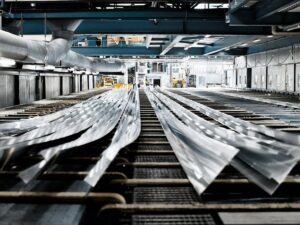
Step#1 Raw Material Preparation and Alloy Design
The first step in the manufacturing process of 6061 aluminum alloy is the preparation of raw materials and the precise design of the alloy composition. Aluminum, the primary component of the alloy, is extracted from bauxite ore through the Bayer process. The extracted aluminum is then refined and purified to remove impurities, resulting in pure aluminum.
Step#2 Melting and Casting
The next step is the melting and casting of the prepared aluminum alloy. The pure aluminum and the alloying elements are combined and melted together in a furnace at high temperatures. The intense heat causes the elements to mix and form a homogenous molten alloy.
Step#3 Heat Treatment and Extrusion
After casting, the 6061 aluminum alloy undergoes a crucial step known as heat treatment. Heat treatment involves subjecting the alloy to a controlled heating and cooling process to improve its mechanical properties. This process enhances the strength, hardness, and overall performance of the alloy.
Main Uses and Applications
6061 aluminum alloy, renowned for its exceptional strength, weldability, and versatility, finds extensive use across a wide range of industries. Let’s explore some of the common uses and applications of 6061 aluminum alloy.
Aerospace and Aviation Industry
6061 aluminum alloy is widely employed in the aerospace and aviation sector due to its high strength-to-weight ratio and excellent machinability. It is used in the production of aircraft structures, such as wings, fuselage panels, and landing gear components. The alloy’s ability to withstand extreme conditions, coupled with its weldability and formability, makes it a preferred choice in the demanding aerospace industry.
Automotive Components and Parts
In the automotive industry, 6061 aluminum alloy is utilized for various components and parts that require strength, durability, and lightweight properties. It is commonly used in the manufacturing of wheel rims, suspension parts, engine blocks, and transmission cases. The alloy’s ability to withstand high stress and its excellent machinability contribute to improved performance and fuel efficiency in automotive applications.
Sporting Goods and Equipment
6061 aluminum alloy finds extensive use in the production of sporting goods and equipment due to its strength, lightweight nature, and corrosion resistance. It is commonly used in the manufacturing of bicycle frames, handlebars, golf club heads, and baseball bats.
Strengths and Weaknesses
6061 aluminum alloy possesses several notable strengths that make it a popular choice across various industries. However, it also has a few limitations that should be considered. Let’s explore the strengths and weaknesses of 6061 aluminum alloy.
Strengths:
- One of the key strengths of 6061 aluminum alloy is its impressive strength-to-weight ratio. It offers high tensile strength while still maintaining relatively low density.
- 6061 aluminum alloy exhibits excellent formability, allowing it to be easily shaped, bent, or formed into various configurations without compromising its strength.
- 6061 aluminum alloy demonstrates good resistance to corrosion, especially when compared to other alloys.
Weaknesses:
- One of the weaknesses of 6061 aluminum alloy is its susceptibility to stress corrosion cracking under certain conditions.
- While 6061 aluminum alloy is generally considered weldable, it can be more challenging to weld compared to other aluminum alloys.
4. Comparison of 5052 and 6061 Aluminum Alloys
Following our detailed discussion on the individual characteristics of both 5052 and 6061 aluminum alloys, it’s beneficial to put them side by side for a comparative analysis. Let us take a look:
Strength and hardness
In terms of absolute strength, 6061 typically comes out on top due to its heat-treatable nature. It undergoes an aging process post heat treatment that greatly enhances its strength. 5052, on the other hand, has a respectable strength that is sufficient for many applications but falls short when compared to 6061.
Corrosion resistance
While both alloys exhibit good corrosion resistance, 5052 is particularly known for its exceptional performance in marine and high saline environments due to the presence of chromium in its composition. 6061, although resistant to general corrosion, may not fare as well as 5052 when exposed to harsh or aggressive conditions, especially those involving seawater or salt spray.
Weldability
At Suproto, both 5052 and 6061 demonstrate good weldability, which means they can be joined using various welding techniques. However, 6061 tends to stand out in this area due to its superior fusion and penetration characteristics. Nonetheless, 5052 doesn’t lag too far behind and can be satisfactorily welded for most applications.
Formability
5052 takes the lead when it comes to formability. Its ability to retain strength while being molded into intricate shapes makes it an ideal choice for applications that require complex design patterns. In contrast, while 6061 is formable, its higher strength may make it less suitable for applications involving intense shaping or bending.
Cost-effectiveness
In terms of cost-effectiveness, both alloys present a good case. While 5052 offers excellent corrosion resistance and formability at a competitive price, 6061 counters with superior strength and weldability at a comparable cost. However, the total cost would also factor in other considerations, like the need for heat treatment in 6061 and the cost of dealing with corrosion in severe environments for 6061.
Machinability
An essential factor to consider when comparing the 5052 and 6061 alloys is their machinability – the ease with which they can be cut and shaped using various machine tools. The 6061 aluminum alloy outshines 5052 in this aspect due to its higher silicon content, which contributes to a lower friction coefficient during machining. This means that 6061 tends to generate less heat, thereby reducing the wear and tear on tools.
Thermal and Electrical Conductivity
Another area where these two alloys diverge is in their thermal and electrical conductivity. Aluminum is generally known for its excellent thermal conductivity, and both 5052 and 6061 are no exception. However, 6061, with its greater copper content, tends to exhibit slightly superior electrical conductivity compared to 5052.
The table below highlights the thermal and electrical conductivity properties of aluminum alloys 5052 and 6061, providing insights into their respective performance in these important areas.
Property |
Aluminum 5052 |
Aluminum 6061 |
Thermal Conductivity |
High |
High |
Electrical Conductivity |
Good |
Better |
5. 7 actors To Consider When Choosing Between 5052 and 6061
Choosing between 5052 and 6061, or any two aluminum alloys, involves multiple considerations that go beyond just their basic properties. Here are the several factors that can affect performance, cost, and the overall success of the project.
#1 Understanding the Application
Understanding the application is the first step in selecting the right aluminum alloy. Anyone will agree that each application will have its unique requirements and challenges. For example, if the application is in a marine environment, 5052 with its superior resistance to saltwater corrosion would be a clear choice.
#2 Mechanical Requirements
The mechanical requirements of the end product play a crucial role in alloy selection. If the product needs to bear high loads or resist impact, an alloy with high strength like 6061 would be preferable. However, if the product requires intricate shaping or deep drawing, an alloy with excellent formability like 5052 would be better suited.
#3 Environmental Conditions
The environmental conditions in which the end product will operate are another vital factor. In a corrosive environment, like the sea, an alloy with high corrosion resistance like 5052 would be an optimal choice. But in a benign environment, other properties like strength or weldability might take precedence.
#4 Manufacturing Process
The manufacturing process, including the choice of alloy, significantly impacts the performance of the Spline Shaft. If the product involves a lot of welding, 6061 with its excellent weldability might be preferred. But if the process involves a lot of forming, then 5052 would be a better choice due to its superior formability.
#5 Cost Considerations
While it’s important to select an alloy based on performance characteristics, cost considerations cannot be ignored. Both the initial cost of the alloy and the total cost of manufacturing need to be considered. For instance, while 6061 might be cheaper upfront, the additional cost of heat treatment might make 5052 more cost-effective overall.
#6 Availability and Lead Time
Lastly, the availability of the alloy and the lead time required for its delivery should be considered. If an alloy is not readily available or requires a long lead time, it might delay the project or increase the cost. Both 5052 and 6061 are widely available due to their popularity, but the need for heat treatment in 6061 might lead to longer lead times.
#7 Project Timeline
The project timeline is an equally significant factor. If the project is time-sensitive, choosing an alloy like 5052 that doesn’t require additional processing (like heat treatment in 6061) could save time and expedite project completion. However, if time allows, opting for an alloy like 6061 that offers superior strength might be worth the extra processing time.
Dive Deeper Into Our Resources
Looking for more diverse service options? Browse through our handpicked selections:
Still haven’t found what you’re looking for? Don’t hesitate to contact us. We’re available around the clock to assist you.
Conclusion
Deciphering the world of aluminum alloys, particularly the popular 5052 and 6061 series, can indeed be a challenging task. Each alloy brings unique properties and benefits to the table, making the selection process a nuanced decision dependent on a multitude of factors. A deep understanding of these alloys, as explained in this comprehensive guide, can pave the way for effective decision-making that aligns with specific projects.
For specialized guidance or to source high-quality 5052 and 6061 aluminum alloys, Suproto, a reputable manufacturer of these materials, stands ready to assist. Contact us today for further information or request a quote by getting in touch with us.